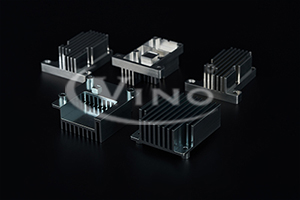
在精密机械零件加工领域,表面质量不仅关乎零件的外观,更对其性能、可靠性和使用寿命有着决定性影响。随着现代制造业对零件精度和质量要求的不断攀升,实现精准的表面质量控制成为了行业焦点。
影响表面质量的因素
切削参数
切削速度、进给量和切削深度是影响零件表面质量的关键切削参数。切削速度过高,易引发积屑瘤,导致零件表面粗糙度增加;进给量过大,会在零件表面留下明显刀痕,同样恶化表面质量;切削深度的选择不当,则可能造成切削力突变,引起振动,影响表面平整度。
刀具因素
刀具的几何形状、材料和磨损程度对表面质量影响显著。刀具的前角、后角和刃倾角决定了切削力的大小和方向,合适的刀具角度能有效降低切削力,减少表面损伤。刀具材料的硬度、耐磨性和热稳定性影响其切削性能,优质刀具材料能保持刀刃锋利,延长刀具使用寿命,保障加工表面质量。而刀具磨损到一定程度后,切削刃变钝,切削力增大,会严重恶化表面质量。
工件材料特性
不同的工件材料因其硬度、韧性、组织结构等特性差异,加工后的表面质量也有所不同。硬度较低的材料,如铝合金,在加工过程中易产生变形和粘刀现象;韧性较好的材料,切削时切屑不易折断,可能缠绕在工件表面,造成划伤;材料内部组织结构不均匀,也会导致加工表面质量不稳定。
加工工艺系统的振动
加工过程中,工艺系统的振动会使刀具与工件之间产生相对位移,在零件表面形成振纹,显著降低表面质量。振动源包括机床自身的振动、切削力的周期性变化以及外界干扰等。
表面质量控制措施 优化切削参数 通过试验和仿真分析,针对不同的工件材料和加工要求,确定最佳的切削参数组合。在保证加工效率的前提下,尽可能降低切削速度,减小进给量和切削深度,以获得良好的表面质量。例如,在精铣铝合金零件时,选择较高的切削速度(200 - 300m/min)、较小的进给量(0.05 - 0.1mm/z)和切削深度(0.1 - 0.3mm),可有效减少表面粗糙度。 选择合适刀具 根据工件材料和加工工艺,挑选适配的刀具。对于硬度较高的材料,可选用硬质合金刀具或陶瓷刀具;加工有色金属时,高速钢刀具可能更为合适。同时,定期对刀具进行刃磨和更换,确保切削刃始终保持锋利状态。如在加工高强度合金钢时,采用涂层硬质合金刀具,能显著提高刀具的耐磨性和切削性能,改善表面质量。 控制工件材料质量 严格把控工件材料的质量,确保其成分和组织结构符合要求。对材料进行适当的预处理,如退火、正火等,改善材料的加工性能。例如,对一些易变形的材料进行预先热处理,消除内部残余应力,可减少加工过程中的变形,提高表面质量。 降低工艺系统振动 采取多种措施抑制工艺系统振动。优化机床结构,提高机床的刚性和稳定性;采用阻尼装置,吸收振动能量;合理安排加工顺序,避免切削力的集中和突变。如在加工细长轴类零件时,使用中心架或跟刀架,增加工件的刚性,减少振动,保证表面质量。 表面质量检测方法 粗糙度测量 采用粗糙度仪对零件表面粗糙度进行测量,通过触针法或光学法获取表面轮廓数据,计算出表面粗糙度参数,如 Ra(轮廓算术平均偏差)、Rz(微观不平度十点高度)等,以此评估表面微观几何形状误差。 表面形貌观察 利用显微镜、扫描电子显微镜(SEM)等设备观察零件表面形貌,直观了解表面是否存在划伤、裂纹、变形等缺陷,分析表面质量状况。 硬度检测 通过硬度测试,检查零件加工表面的硬度是否符合要求,判断加工过程是否对表面硬度产生影响,进而评估表面质量。常见的硬度测试方法有洛氏硬度、布氏硬度和维氏硬度测试等。
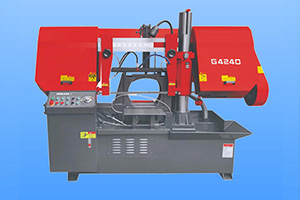
精密机械零件加工的表面质量控制是一个系统工程,涉及加工过程的各个环节。只有全面了解影响表面质量的因素,采取有效的控制措施,并借助精准的检测手段,才能确保加工出高质量的精密机械零件,满足现代制造业不断发展的需求。