在机械制造领域,材料的选择对于精密机械零件加工的质量、性能及成本起着决定性作用。高碳钢作为一种常见的金属材料,其是否适用于精密机械零件加工,一直是业内关注与探讨的焦点。
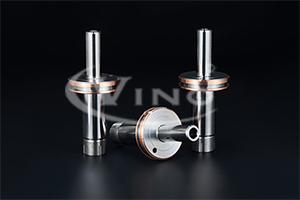
高碳钢的特性剖析
高碳钢含碳量通常在 0.60% - 1.70% 之间。较高的含碳量赋予了它一系列独特的性能。首先,高碳钢具有出色的硬度与强度。经过适当的热处理后,其硬度可显著提升,能够承受较大的压力与磨损,这使得它在一些对耐磨性能要求较高的场合具有优势,例如模具制造、刀具生产等。其次,高碳钢具备良好的切削加工性。在一定条件下,刀具可以较为顺畅地对其进行切削,形成所需的形状和尺寸。然而,高碳钢也存在一些固有缺点。由于含碳量高,其韧性相对较低,在受到冲击载荷时容易发生脆性断裂。而且,高碳钢在热处理过程中,变形倾向较大,这对于精密加工来说是一个不容忽视的挑战。
精密机械零件加工与精密机械零部件加工对精度、表面质量和材料性能稳定性有着极高的要求。精度方面,往往需要达到微米甚至纳米级别,任何微小的尺寸偏差都可能影响整个机械系统的运行性能。表面质量上,要求零件表面光滑,粗糙度低,以减少摩擦损耗、提高零件的耐磨性和耐腐蚀性。材料性能稳定性也至关重要,零件在不同的工作环境和使用周期内,其力学性能、尺寸稳定性等应保持相对稳定,确保机械系统的可靠运行。 高碳钢在精密机械零件加工中的适用性分析
优势体现
满足特定耐磨需求:对于一些如精密模具、精密传动部件等对耐磨性要求极高的精密机械零件,高碳钢的高硬度和良好的耐磨性使其成为可选材料之一。例如,在注塑模具的制造中,高碳钢经过淬火、回火等热处理工艺后,能够长时间承受塑料熔体的冲刷和摩擦,保证模具的尺寸精度和表面质量,从而生产出高精度的塑料制品。
可加工性利于成型:高碳钢相对较好的切削加工性,使得在精密加工过程中,可以通过各种切削工艺,如车削、铣削、磨削等,将其加工成复杂的形状和精确的尺寸。熟练的加工工人和先进的加工设备配合,可以充分发挥高碳钢的可加工性优势,实现精密零件的成型。
面临挑战
热处理变形问题:如前文所述,高碳钢在热处理过程中变形倾向较大。而精密机械零件对尺寸精度要求极高,热处理引起的哪怕是微小的变形,都可能导致零件尺寸超差,无法满足设计要求。例如,在制造精密齿轮时,热处理后的变形可能使齿轮的齿形精度下降,影响齿轮传动的平稳性和准确性。为解决这一问题,需要在热处理工艺上进行优化,采用先进的淬火、回火工艺,如分级淬火、等温淬火等,并配合合适的工装夹具,尽量减少变形量。同时,在加工过程中,要预留适当的加工余量,以便在热处理后通过后续加工修正尺寸。
韧性不足风险:高碳钢韧性较低,在精密机械零件承受冲击或振动载荷时,存在脆性断裂的风险。对于一些在复杂工况下工作的精密零件,如航空发动机中的某些精密传动零件,这种脆性断裂可能会引发严重的安全事故。为提高高碳钢的韧性,可以通过适当的合金化处理,添加如铬、镍、钼等合金元素,改善其组织结构,提高韧性。此外,在零件设计时,应充分考虑其受力情况,合理优化结构,避免应力集中,降低脆性断裂的可能性。
结论
高碳钢材料在精密机械零件加工中具有一定的适用性,但并非适用于所有类型的精密机械零件。在一些对耐磨性要求高、形状相对简单且对韧性要求不是特别苛刻的精密零件加工中,高碳钢能够发挥其优势。然而,在面对对尺寸精度、韧性和稳定性要求极高的复杂精密机械零件加工时,高碳钢的局限性较为明显。在实际应用中,需要综合考虑零件的具体使用要求、加工工艺的可行性以及成本等多方面因素,权衡高碳钢材料的利弊,选择最为合适的材料,以确保精密机械零件的加工质量和性能满足设计要求。同时,随着材料科学和加工技术的不断发展,对高碳钢材料的改性和加工工艺的优化,有望进一步拓展其在精密机械零件加工领域的应用范围。